1 Introduction
XK7136 vertical machining center, original CNC servo system and DC servo motor of American AB company; the capacity of rotary table tool magazine is 16 knives, automatic tool change by pneumatic device; spindle is the analog servo spindle of INDRAMAT company of Germany. There are three shortcomings in the original control system of the machining center: (1) Due to the influence of the external environment, the analog signal is greatly disturbed, and because the machine tool is semi-closed loop control, the positioning accuracy is not high, so the machining accuracy of the machine tool is not high; (2) When changing the knife to find the knife, the number of rotation steps of the cutter head is calculated by the absolute method, so that the knife is occupied for a long time; (3) the spindle is controlled by an external circuit, and there is no communication with the system, and the control is inconvenient. After the transformation of SKY numerical control system, the high precision, high speed and easy control of machine tool processing are realized.
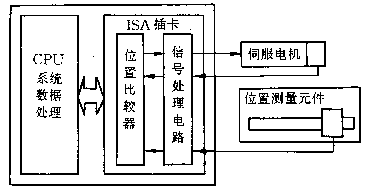 Figure 1 signal processing box
|
2 modification of the servo system
SKY CNC system is a CNC system developed on the PC platform. It realizes signal conversion, input and output through the ISA multi-function card of PC. In the transformation of the machine tool, the SKY system's unique two-position closed-loop control method is adopted, and the servo unit uses a digital AC servo motor (Fig. 1). The two-position closed loop overcomes the nonlinear effect of the general full-closed loop (speed loop + position loop) and does not produce self-sustaining oscillations and cannot work. It is composed of a position detecting component (grating scale) and a position comparator of the ISA card to form a position outer ring, and a corner-line displacement double formed by the position inner ring formed by the position comparator of the servo motor with the photoelectric code disk and the ISA card. Closed loop system. Since the inner ring of the corner constitutes a follower system, when the system displacement command is issued, the position detecting component of the outer position ring directly acquires the displacement information of the table, and the servo motor drives the table through the followability of the inner ring. The system compares the feedback value of the raster with the command value through the position comparison circuit of the ISA card, and controls the difference with the comparison until the difference is eliminated. At this time, the feedback value of the grating is equal to the command value, which theoretically eliminates the influence of the machine gap on the accuracy. The accuracy of the scale is 5μm, and the machining accuracy of the machine tool is very high. The advantage of using a digital AC servo motor is its strong anti-interference ability. After the command signal is sent in the form of a binary code, it is transmitted as a set of pulse signals, which is not easily interfered by the external environment, and the binary code is transmitted in the form of a detection code to ensure the correctness of the binary code.
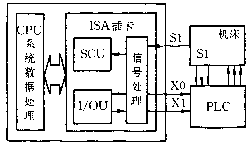 S1. Sensor on the rotary cutter (proximity switch) SCU. Cutter rotation step calculation circuit I/OU. Communication interface between PC and external equipment figure 2
|
Table 1 (X0, X1) | Cutter rotation | 0,1 | Forward | 1,0 | Reverse | 0,0 | stop | |
Table 2 R2- * R1 | Cutter rotation direction | Cutter rotation steps | [0,8] | Positive | R2-R1 | [8,15] | Reverse | 16-(R2-R1) | [-8,0] | Reverse | |R2-R1| | [-8,-15] | Positive | 16-|R2- R1| | |
3 Reform of tool change control
The automatic tool changer (ATC) of the machine tool pneumatically realizes the upper, lower, left and right movement of the rotary table type magazine and the tight/loose knife of the clamping/releasing device. The rotation of the cutter head is achieved by the principle of the Markov wheel transmission.
- Hardware circuit design for finding a knife
In the control of the tool change, we have done the following processing on the ISA card (Figure 2). When the tool change command M06 TXX is issued, the system program judges the rotation direction of the cutter head based on the current tool number and the target tool number of the command and calculates the number of rotation steps. Then, the control signals X0 and X1 are sent to the PLC through the low I/OU to control the forward and reverse rotation of the rotary electric machine (the control states of X0 and X1 are as shown in Table 1). Each time the cutter head rotates one tool number, the proximity switch S1 will send a signal S1 to the SCU, and the SCU counts once. When the SCU count value is equal to the required number of rotation steps, the cutter head is turned to the target tool number, and the system program controls I/. The OU outputs a control signal (0, 0) to the PLC to stop the cutter rotation motor.
- Algorithm for finding a knife program
The 16 tool holder numbers of the rotary cutter are numbered from 1 to 16. Assume that the current tool number is stored in the power-down protection register R1: the target tool number of the instruction is stored in register R2. Then the number of steps that should be rotated is n=|R2- * R1|(n[0,15]). However, if n>8, the number of rotation steps is not the minimum number of steps, so the direction of rotation of the cutter head must be changed, and the number of rotation steps is 16-|R2-R1| (Table 2). According to this algorithm, the number of steps required for the minimum rotation of the cutter head and the direction of rotation of the cutter head can be calculated.
When the system receives the M06 TXX command, the system program first compares R2 with R1, n=R2- * R1. If n=0, then M06 is completed; if n≠0, the system starts to judge the rotation direction of the cutter head and counts the number of rotation steps of the cutter head, and returns the Z axis to the tool change point. Then the system sends a signal to the PLC to control the positioning of the spindle, the upper, lower, left and right movement of the cutter head and the action of the knife/knife.
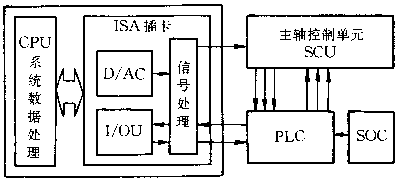 D/AC. Digital/analog conversion circuit SOC. Spindle speed multiple circuit SCU. Spindle control unit image 3
|
4 Transformation of the spindle control part
It is an indispensable step to modify the spindle control part by communicating the SKY numerical control system with the INDRAMAT analog servo spindle control unit. The implementation of the communication is also done by the ISA card and PLC connected to the spindle control unit (Figure 3). When the system receives the spindle rotation command, the system sends a binary digit (in the form of complement code, easy to judge its positive and negative) to the ISA card D/AC according to the product of the commanded rotation speed and the multiple of the spindle spindle speed. The analog signal is output to the SCU. The system sends out a 32-bit binary number, D/AC is converted into an analog signal of +10~-10. The speed is determined by the maximum speed v
s max set in the SCU and the current analog voltage value U. The calculation formula is: v
s =U*v
s max/10. When the U value is positive, the spindle rotation direction is clockwise; when the U value is negative, the spindle rotation direction is counterclockwise. When the system receives the command M03 SXXXX, the command value is positive, the U value is positive, the spindle rotates clockwise; if the command is M04 SXXXX, the command value is negative, the U value is negative, and the spindle rotates counterclockwise.
The PLC controls certain switching signals in the SCU of the spindle control unit, such as the spindle enable signal. When the system receives the M03 or M04 command, the I/OU sends a signal to the PLC. The PLC makes the spindle enable signal high and the spindle rotates.
After the transformation of the SKY numerical control system, this machining center improves the machining accuracy and the tool change speed. The spindle control is more convenient and the spindle speed deviation is reduced.